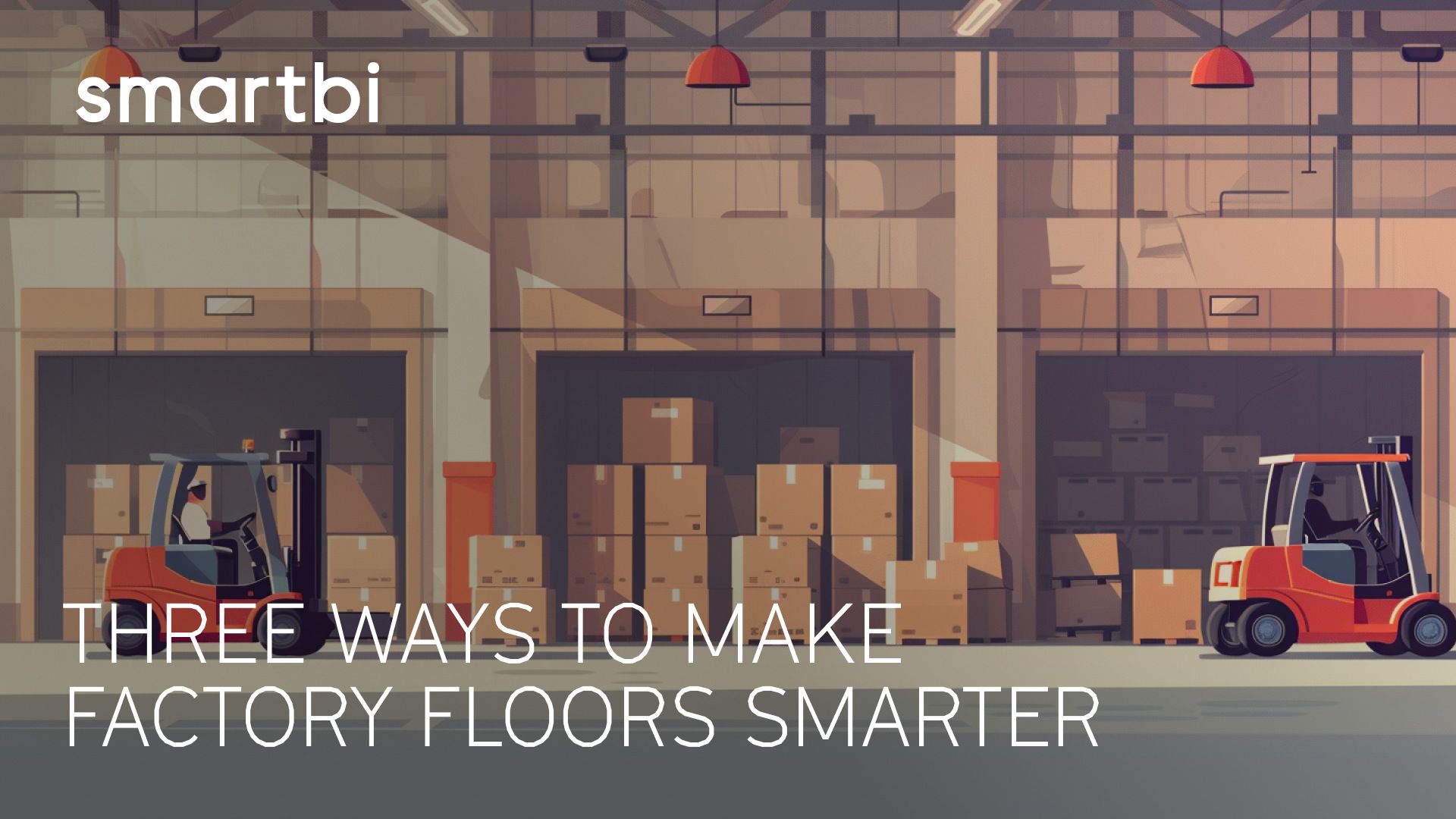
In traditional and surprisingly, in many 21st-century factories, technicians still manually check gauges, fill out forms, and document errors and maintenance histories. These methods are not only tedious but also prone to errors and inaccuracies. Integrating data and analytics into operations has become essential as we enter the 4.0 Industrial Revolution.
In today's competitive manufacturing landscape, staying ahead requires adopting intelligent technologies to optimize processes, improve efficiency, and reduce downtime. Here are three easy ways to make your production or assembly line smarter by leveraging the latest technologies.
Predictive analytics and maintenance: From reactive to proactive
Traditional and modern factory floors generate huge amounts of data, but unfortunately, this data often remains still to this day – underutilized. An effective way to harness this data is through predictive analytics. By using algorithms trained on historical data, predictive analytics can forecast when machinery is likely to malfunction or experience downtime. According to a Deloitte report, predictive maintenance strategies can result in significant benefits such as saving 5%–10% on material cost, 5%–20% reduced inventory carrying costs, 10%–20% increased equipment uptime and availability, and 20%–50% reduction on maintenance planning time.
Example: Škoda Auto has improved its production line maintenance by adopting a predictive maintenance solution with AWS. The new approach uses AI and computer vision to monitor and analyze equipment data, preventing breakdowns and reducing downtime. The solution employs six cameras and artificial neural networks to collect and process data from the production line, identifying potential issues such as loose bolts or dirt in power lines. Škoda highlights this improvement's critical importance: "When a single minute of lost production costs automotive manufacturers the revenue of one car, there's no room for production downtime."
Upgraded sensor technology to smart: Better understanding of the shop floor
Sensors have always played a critical role in manufacturing by providing real-time data on all the possible aspects of production, including temperature, pressure, vibration, and other parameters. Upgrading sensor technology involves connecting all sensors and implementing sensor fusion on a single dashboard to make sense of the data and generate actionable insights.
The latest technologies offer industrial companies an opportunity to improve sensor technology further by integrating advanced capabilities such as microprocessors, storage, diagnostics, and connectivity tools. In addition, we have seen more use cases where companies want to bring all the sensor information under one umbrella, a unified dashboard, and add intelligence that helps them make sense of the numbers and data by building suggested activities and alerts around them. These advancements transform raw sensor data into digital insights, facilitating better decision-making and process optimization across the supply chain.
Example: PepsiCo has a vast network of manufacturing facilities where thousands of machines operate daily, producing snacks and beverages. Monitoring machine health and predicting failures is crucial to prevent costly downtimes and supply chain disruptions. With AI-powered sensors, PepsiCo uses an advanced system that "listens" to machines by analyzing vibration, temperature, and magnetic emissions data. This enables real-time diagnostics and predictive maintenance, allowing the company to address potential issues like bearing wear, gear faults, or structural looseness weeks or months in advance, optimizing machine performance, reducing waste, and ensuring continuous production.
Pushing digitalization further with LLMs: Smart assistant at your disposal
Transitioning from paper-based work instructions to digital versions has become standard practice. Digitalizing work-related instructions and manuals allows easy updates and real-time distribution, ensuring all employees can access the most up-to-date procedures and instructions. However, the rapid evolution of LLMs is taking digitalization to the next level by transforming static digital information into actionable insights.
LLMs can significantly improve human-machine interaction by translating complex sensor data into understandable reports and alerts. Companies can for example use LLMs to develop digital forms that suggest possible answers based on historical data, reducing employees' time filling out repetitive information. Additionally, LLMs can analyze task dependencies and send automated notifications to the next responsible party, streamlining workflows and reducing bottlenecks.
Example: Morgan Stanley has an extensive content library containing investment strategies, market research, and analyst insights. The information, mainly in PDF form, requires advisors to search it extensively. With GPT-4, Morgan Stanley uses an internal chatbot to access and synthesize this data, assisting in advisor-client interactions instantly. In an industrial context, a similar approach can be used when responding to operators' natural language queries (imagine an intelligent, up-to-date assistant at your disposal on the shop floor), making it easier for non-experts to understand and act on sensor data. This capability streamlines workflows and improves access to different data sources, leading to better decision-making across the organization.
Contact usCould AI be applied to your business case?
Subscribe to the newsletter and learn how AI can solve business challenges.